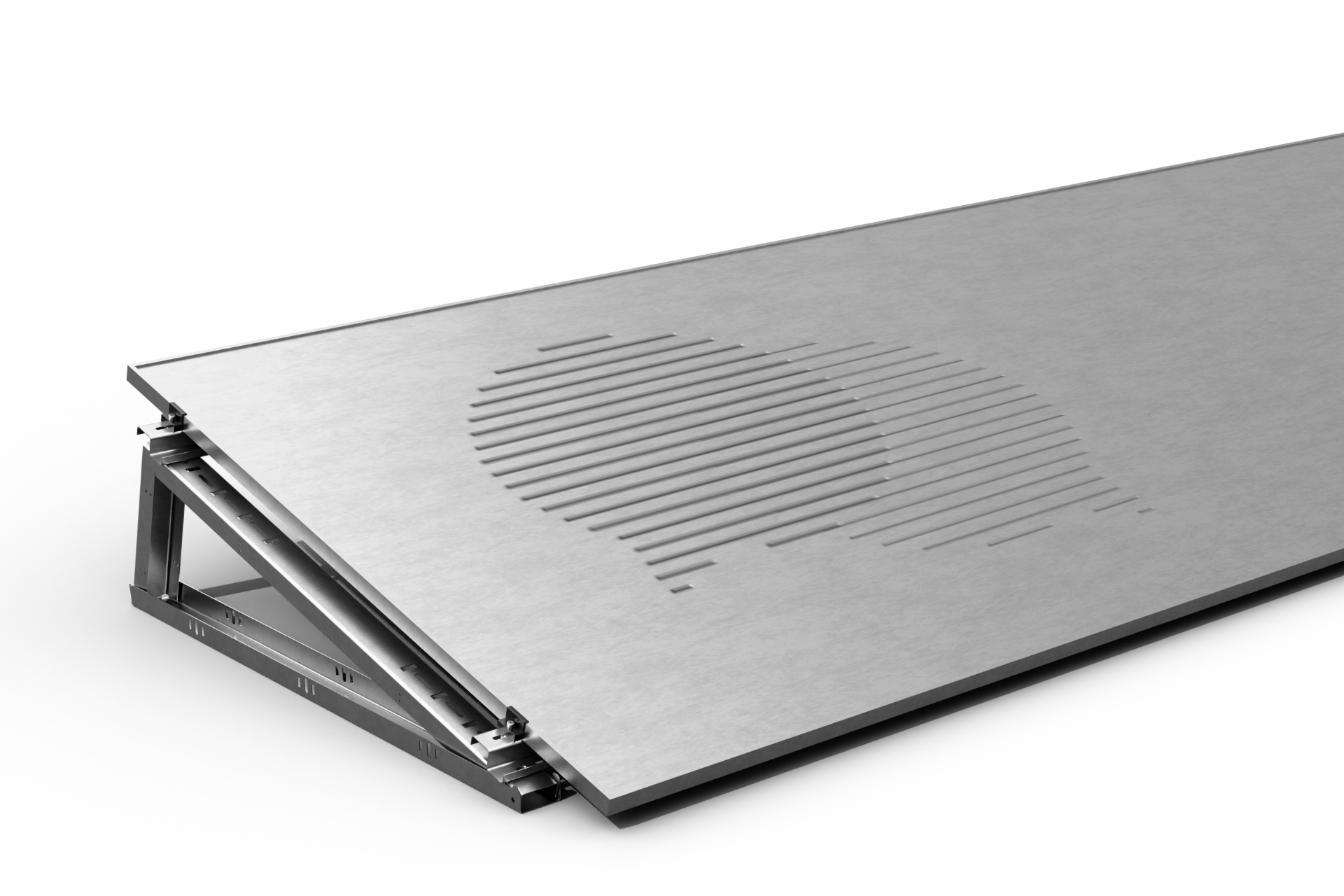
FAQ
PG Group przeszło wszystkie kroki potrzebne do spełnienia warunków normy środowiskowej ISO 14001 i posiada certyfikację. Aby uzyskać normę środowiskową ISO 14001, firma musiała spełnić następujące warunki:
Wdrożenie Systemu Zarządzania Środowiskowego (SZŚ)
- Przeprowadzenie audytu wstępnego w celu oceny obecnego stanu organizacji.
- Opracowanie i wdrożenie udokumentowanego systemu SZŚ, w tym:
- Polityki środowiskowej
- Procedur systemowych
- Instrukcji operacyjnych
- Identyfikacja i ocena aspektów środowiskowych związanych z działalnością firmy.
- Określenie celów i zadań środowiskowych zgodnych z polityką firmy.
- Zapewnienie zgodności z obowiązującymi przepisami prawnymi dotyczącymi ochrony środowiska.
Funkcjonowanie systemu
- Zapewnienie zaangażowania kierownictwa w budowanie i utrzymanie SZŚ.
- Wdrożenie podejścia procesowego i cyklu PDCA (Planuj-Wykonaj-Sprawdź-Działaj).
- Prowadzenie monitoringu i pomiarów kluczowych parametrów środowiskowych.
- Szkolenie pracowników z zakresu wymagań normy ISO 14001 i wdrożonych procedur.
- Wdrożenie sterowania operacyjnego dla procesów związanych ze znaczącymi aspektami środowiskowymi.
- Opracowanie i wdrożenie procedur reagowania na sytuacje awaryjne.
Certyfikacja
- Przeprowadzenie audytu wewnętrznego w celu weryfikacji zgodności z wymaganiami normy.
- Podjęcie działań korygujących i zapobiegawczych w przypadku wykrycia niezgodności.
- Przejście audytu certyfikującego przeprowadzonego przez akredytowaną jednostkę certyfikującą.
PG Group spełnia wymagania zgodne z normą EN 1090 i posiada certyfikację Firma musiała przejść przez następujące etapy:
Wdrożenie Systemu Zakładowej Kontroli Produkcji (ZKP)
- Opracowanie i wdrożenie udokumentowanego systemu Zakładowej Kontroli Produkcji (ZKP).
- System ZKP powinien obejmować wszystkie procesy specjalne stosowane w produkcji, takie jak:
- Projektowanie (jeśli firma prowadzi taki proces)
- Spawanie
- Zabezpieczenie przed korozją
- Łączenie z wykorzystaniem łączników mechanicznych
- Kontrola i badania
- Zapewnienie odpowiedniego personelu, wyposażenia i procedur dla zapewnienia zgodności wyrobu.
Spełnienie wymagań technicznych
- Spełnienie wymagań technicznych określonych w normie EN 1090-2 dla konstrukcji stalowych lub EN 1090-3 dla konstrukcji aluminiowych.
- Przeprowadzenie pierwszego badania typu (ITT) i pierwszych obliczeń typu (ITC) dla produktów.
- Zapewnienie jakości spawania zgodnie z normą ISO 3834 (część 2, 3 lub 4).
Certyfikacja
- Przejście wstępnej inspekcji zakładowej kontroli produkcji przeprowadzonej przez akredytowaną jednostkę notyfikowaną.
- Pozytywne przejście audytu certyfikującego obejmującego pełny zakres systemu ZKP.
- Uzyskanie certyfikatu systemu Zakładowej Kontroli Produkcji oraz Certyfikatu dla Spawalnictwa.
Dodatkowe wymagania
- Posiadanie wykwalifikowanego personelu, w tym spawaczy z odpowiednimi uprawnieniami.
- Zapewnienie odpowiedniego wyposażenia do produkcji, pomiarów i kontroli.
- Wdrożenie systemu nadzoru nad dokumentacją i zapisami.
- Opracowanie i stosowanie procedur oceny zgodności wyrobu.
Obecny certyfikat zgodności z normą EN 1090 jest ważny do 12.12.2026 r.
Perforacja blachy to proces tworzenia regularnych otworów w blachach metalowych, które mogą mieć różne kształty, rozmiary i wzory. Otwory te są zwykle rozmieszczone w ustalonym układzie (np. rzędowym, mijankowym lub innym). Perforacja jest wykonywana w celu nadania blachom określonych właściwości funkcjonalnych, estetycznych lub technologicznych.
Cechy perforacji:
- Kształt otworów: Okrągłe, kwadratowe, prostokątne, sześciokątne, dekoracyjne (np. wzory nieregularne).
- Układ otworów: Regularny (symetryczny) lub nieregularny, w rzędach prostych lub przesuniętych.
- Wielkość otworów: Od bardzo drobnych (np. poniżej 1 mm) po duże (kilka centymetrów).
- Stopień perforacji: Procentowy udział powierzchni otworów w całkowitej powierzchni blachy.
Metody perforacji blachy:
- Mechaniczna (prasa perforacyjna):
- Najczęściej stosowana metoda w przemyśle, wykorzystująca matryce i stemple.
- Laserowa:
- Umożliwia precyzyjne wycinanie dowolnych wzorów, szczególnie w produkcji niestandardowej.
- Wodne cięcie (hydro cutting):
- Używane do skomplikowanych kształtów i materiałów trudnych do obróbki.
- Chemiczna (trawienie):
- Stosowana głównie w przypadku cienkich blach i delikatnych wzorów.
Zastosowania perforowanych blach:
- Wentylacja i przepuszczalność:
- W systemach wentylacyjnych, klimatyzacyjnych i filtracyjnych.
- Design i architektura:
- Fasady budynków, ekrany akustyczne, sufity podwieszane, balustrady, elementy dekoracyjne.
- Przemysł i technologia:
- Sita w maszynach, osłony, podesty robocze, panele akustyczne.
- Zastosowania ochronne:
- Kraty ochronne, osłony maszyn, zabezpieczenia antywłamaniowe.
- Rolnictwo i przemysł spożywczy:
- Elementy maszyn do sortowania, suszenia lub obróbki produktów.
Dzięki perforacji blacha może łączyć lekkość z wytrzymałością i funkcjonalnością, co czyni ją niezwykle wszechstronnym materiałem.
W naszej ofercie posiadamy usługi spawalnicze różnymi metodami. W zależności od potrzeb klienta jesteśmy w stanie zaoferować spawanie metodami: TIG, MIG/MAG i spawanie elektrodą.
Maksymalna grubość cięcia laserem zależy od rodzaju materiału:
- Stal nierdzewna: 30 mm
- Stal węglowa: 25 mm
- Aluminium: 25 mm
- Miedź: 15 mm
Te wartości są osiągalne na maszynie TruLaser 3060, która oferuje największe możliwości cięcia spośród wymienionych urządzeń.
Dla blachy o grubości 2 mm, maksymalna długość gięcia wynosi 8300 mm. Jest to możliwe na maszynie VarioPress 300-80, która ma maksymalną długość gięcia 8300 mm i może obsługiwać materiały o grubości do 4,0 mm.
Blacha ocynkowana i blacha w powłoce cynkowo-magnezowej różnią się kilkoma istotnymi cechami:
Skład powłoki
- Blacha ocynkowana: Pokryta jest warstwą czystego cynku.
- Blacha cynkowo-magnezowa: Powłoka składa się z cynku z dodatkiem magnezu, co zapewnia lepsze właściwości ochronne.
Odporność na korozję
- Blacha ocynkowana: Zapewnia dobrą ochronę przed korozją, ale jest podatna na uszkodzenia powłoki podczas transportu i montażu.
- Blacha cynkowo-magnezowa: Posiada znacznie lepszą odporność na korozję niż blacha ocynkowana.
Trwałość
- Blacha ocynkowana: Ma krótszą żywotność w porównaniu do blachy cynkowo-magnezowej.
- Blacha cynkowo-magnezowa: Charakteryzuje się dłuższą żywotnością i lepszą ochroną podłoża stalowego.
Grubość i masa powłoki
- Blacha ocynkowana: Wymaga grubszej powłoki dla zapewnienia odpowiedniej ochrony.
- Blacha cynkowo-magnezowa: Osiąga porównywalne lub lepsze właściwości ochronne przy mniejszej grubości i masie powłoki.
Odporność na działanie czynników atmosferycznych
Blacha cynkowo-magnezowa wykazuje lepszą odporność na działanie mgły solnej, wilgoci i dwutlenku siarki w porównaniu do blachy ocynkowanej.
Termin realizacji jest określany na podstawie wielu czynników takich jak: złożoność projektu, skomplikowanie technologiczne, wolumen produkcji oraz aktualny plan produkcyjny zakładu. Każdy projekt traktowany jest indywidualnie. Czas może znacznie się różnić i wynosić od 1 do 4 tygodni.
W przypadku działalności usługowej zakładu produkcyjnego w Nowej Wsi Wrocławskiej skupiamy się na współpracach B2B. Kooperujemy z wieloma firmami od mikroprzedsiębiorstw po największe globalne korporacje. Nie mamy ustalonego MOQ, ale wszystko zależy od indywidualnego projektu.
Czas realizacji zamówienia zależy od tego, czy jest to indywidualny projekt „szyty na miarę” , czy jest to zamówienie standardowe, którego elementy znajdują się na magazynie. W przypadku zamówienia konstrukcji standardowej czas ogranicza się tylko do czasu przeprocesowania zamówienia i czasu wysyłki. W przypadku dużych projektów indywidualnych czas realizacji to zazwyczaj kilka tygodni, w zależności od stopnia przygotowania niezbędnych informacji przez klienta.
pokrytej cynkowo-magnezowymi powłokami antykorozyjnymi np. Magnelis lub POSMAC
Standardowo konstrukcje wykonywane są ze stali konstrukcyjnej S350GD. Jest to odmiana powlekana metalicznie, która charakteryzuje się wysoką wytrzymałością i odpornością na korozję.
Właściwości mechaniczne
- Granica plastyczności (Re): ≥350 MPa
- Wytrzymałość na rozciąganie (Rm): ≥420 MPa
- Wydłużenie przy zerwaniu (A80): ≥16% (dla grubości 0.7-6 mm)
Kąt nachylenia konstrukcji zależny jest od dobranej konstrukcji. Zazwyczaj wynosi on od kilkunastu do kilkudziesięciu stopni. Zależy on od rodzaju konstrukcji i jej konfiguracji. Kąty mogą być stałe lub regulowane.
Każda instalacja wymaga indywidualnej oceny przed realizacją, w szczególności określania maksymalnego obciążania dachu, stanu faktycznego dachu i jego poszycia, oraz analizy siły wiatru i obciążenia śniegiem. Dopiero po wykonaniu pełnej analizy jesteśmy w stanie określić, czy dany dach nadaje się do instalacji fotowoltaiki.
System zgrzewany do membrany lub papy bitumicznej.
- Palowanie
- Betonowanie
- Przykręcanie do balastu
- Regularne przeglądy: Przeprowadzanie regularnych kontroli technicznych instalacji.
- Czyszczenie paneli: Usuwanie zanieczyszczeń z powierzchni paneli, takich jak kurz, liście czy śnieg.
- Monitorowanie wydajności: Śledzenie wydajności systemu, aby wykryć ewentualne problemy i zoptymalizować produkcję energii.
- Wytrzymałość dachu: Dach musi być w stanie wytrzymać dodatkowy ciężar paneli i konstrukcji.
- Kąt nachylenia: Dach powinien mieć odpowiedni kąt nachylenia do optymalnego wykorzystania energii słonecznej.
- Brak zacienienia: Dach powinien być wolny od zacienienia przez inne części budynku, drzewa czy inne przeszkody.
- Stabilne fundamenty: Konstrukcja musi być stabilna, aby wytrzymać warunki atmosferyczne, takie jak wiatr i opady.
- Wystarczająca przestrzeń: Należy zapewnić odpowiednią ilość miejsca na działce, aby zmieścić panele.
- Brak zacienienia: Obszar powinien być wolny od zacienienia przez drzewa czy budynki, aby maksymalnie wykorzystać promieniowanie słoneczne.
- Oszczędność miejsca: Instalacja na dachu nie zajmuje dodatkowej przestrzeni na działce.
- Mniejsze ryzyko kradzieży: Panele na dachu są trudniejsze do kradzieży niż te na gruncie.
- Zwiększona estetyka: Panele mogą być dyskretnie zamontowane i mniej widoczne z poziomu ziemi.
- Lepsza wentylacja: Panele zamontowane na gruncie mają lepszą wentylację, co może zwiększyć ich wydajność.
- Elastyczność ustawienia: Możliwość ustawienia paneli pod optymalnym kątem i kierunkiem.
- Łatwiejszy dostęp do konserwacji: Większa dostępność do paneli ułatwia konserwację i naprawy.
Konstrukcje dachowe to systemy montażowe stosowane do instalacji paneli fotowoltaicznych na dachach budynków. Konstrukcje te są dostosowane do różnych typów dachów, takich jak dachy płaskie, skośne czy blaszane.
Konstrukcje gruntowe to systemy montażowe używane do instalacji paneli fotowoltaicznych na otwartych przestrzeniach, takich jak pola czy nieużytki. Są one stabilizowane za pomocą fundamentów betonowych lub śrub ziemnych.
Instalacja fotowoltaiczna, zaprojektowana i wykonana przez doświadczoną firmę z użyciem paneli, falowników, osprzętu elektrycznego i kabli solarnych wysokiej jakości, jest bardzo bezpiecznym urządzeniem elektrycznym. Ryzyko porażenia prądem lub pożaru najczęściej wynika z błędów w projekcie lub montażu. Przepisy PPOŻ. znowelizowane 19 sierpnia 2020 roku zwiększyły restrykcje, zmniejszając ryzyko niewłaściwego wykonania instalacji. Zgodnie z nowymi przepisami, każda instalacja o mocy powyżej 6,5 kWp wymaga uzgodnienia projektu z rzeczoznawcą ds. zabezpieczeń przeciwpożarowych oraz powiadomienia Państwowej Straży Pożarnej.
Aby odpowiednio zaprojektowana i zainstalowana instalacja fotowoltaiczna działała bezawaryjnie przez 25-30 lat, należy dokonać odpowiednich wyborów. Właściwy wybór instalatora i komponentów fotowoltaicznych najwyższej jakości, pochodzących ze sprawdzonej hurtowni, gwarantuje wieloletnią sprawność instalacji oraz wysokie oszczędności na energii elektrycznej.
Przed założeniem fotowoltaiki na domu, budynku firmowym lub gospodarstwie rolnym, warto:
- Zweryfikować wiarygodność i opinie firmy instalatorskiej: renomowana firma przygotuje instalację z dbałością o wszystkie detale i zgodnie z normami.
- Upewnić się w kwestii referencji: warto sprawdzić najnowsze zdjęcia z realizacji, aby mieć pewność, że instalator ma profesjonalne ekipy monterskie.
- Wybrać profesjonalnego dostawcę komponentów fotowoltaicznych i elektrycznych: przed zakupem warto przeanalizować ofertę hurtowni fotowoltaicznej, sprawdzić oferowane modele paneli, falowników i systemów zabezpieczeń PV. Ważne jest, aby komponenty miały certyfikaty zgodności z normą europejską.
- Zadbać o pełną i profesjonalną opiekę posprzedażową: to gwarancja, że w razie awarii otrzymasz potrzebne wsparcie techniczne i serwisowe, a Twoje zgłoszenie zostanie szybko rozpatrzone.
Dzięki tym krokom, możesz być pewien, że Twoja instalacja fotowoltaiczna będzie działała sprawnie i przyniesie oczekiwane oszczędności.
Konstrukcje fotowoltaiczne dedykowane panelom monofacjalnym i bifacjalnym różnią się w kilku kluczowych aspektach:
- Sposób montażu
Konstrukcje dla paneli monofacjalnych: Mogą być montowane bezpośrednio na powierzchni dachu lub gruntu, bez konieczności zapewnienia dostępu do światła od spodu.
Konstrukcje dla paneli bifacjalnych: Wymagają specjalnego montażu, który umożliwia dostęp światła do obu stron panelu. Często są instalowane np. na podwyższonych konstrukcjach. - Materiały podłoża
Dla paneli monofacjalnych: Rodzaj podłoża nie ma znaczącego wpływu na wydajność. Dla paneli bifacjalnych: Wymagane jest podłoże o wysokim współczynniku odbicia światła, takie jak biała farba czy beton, aby zwiększyć efektywność paneli. - Kąt nachylenia i orientacja
Panele monofacjalne: Zazwyczaj montowane pod optymalnym kątem w kierunku południowym. Panele bifacjalne: Mogą być ustawiane pionowo wschód-zachód lub standardowo w kierunku południowym. - Wykorzystanie przestrzeni
Panele monofacjalne: Wymagają większej powierzchni dla osiągnięcia tej samej mocy.
Panele bifacjalne: Pozwalają na lepsze wykorzystanie przestrzeni dzięki wyższej wydajności z jednostki powierzchni.
Profile zimnogięte znajdują szerokie zastosowanie w wielu dziedzinach przemysłu i budownictwa:
1. Konstrukcje stalowe:
- Szkielety budynków: Hale magazynowe, przemysłowe, obiekty handlowe, sportowe.
- Konstrukcje dachowe: Wiązary dachowe, płatwie, rygle, elementy nośne.
- Ściany działowe: W konstrukcjach lekkich, np. w systemach suchej zabudowy (profile typu C i U).
- Konstrukcje tymczasowe: Namioty magazynowe, rusztowania, baraki budowlane.
2. Budownictwo mieszkalne:
- Domy szkieletowe: Profile zimnogięte są stosowane jako elementy nośne w lekkim budownictwie stalowym.
- Obudowy dachów: Podparcie dla blach trapezowych, płyt warstwowych lub innych pokryć dachowych.
- Stropy i poddasza: Jako elementy wsporcze przy konstrukcji stropów drewnianych i poddaszy użytkowych.
3. Infrastruktura transportowa:
- Konstrukcje mostowe: Elementy wzmacniające i konstrukcyjne mostów.
- Elementy barier ochronnych: Profile wykorzystywane w barierach drogowych i kolejowych.
4. Przemysł i logistyka:
- Regały magazynowe: Lekkie i wytrzymałe elementy regałów stalowych.
- Konstrukcje urządzeń przemysłowych: Obudowy i szkielet maszyn.
- Kontenery i opakowania stalowe: Konstrukcje nośne pojemników transportowych.
5. Energetyka i fotowoltaika:
- Konstrukcje wsporcze: Stelaże pod panele fotowoltaiczne i systemy solarne.
- Wieże i maszty: Elementy konstrukcji słupów energetycznych i masztów komunikacyjnych.
6. Zastosowania architektoniczne:
- Elewacje budynków: Profile jako podkonstrukcja pod panele elewacyjne.
- Wiaty i zadaszenia: Lekkie konstrukcje wiat przystankowych, zadaszeń tarasów czy parkingów.
7. Rolnictwo:
- Konstrukcje obiektów rolniczych: Hale, wiaty na maszyny rolnicze, stodoły.
- Silosy i zbiorniki: Elementy konstrukcyjne zbiorników na zboże czy pasze.
Profile zimnogięte cieszą się popularnością ze względu na ich wszechstronność i możliwość dostosowania do specyficznych wymagań projektu.
Profile zimnogięte charakteryzują się wysoką wytrzymałością, co jest jedną z ich kluczowych zalet. Oto najważniejsze informacje dotyczące wytrzymałości profili zimnogiętych:
- Wysoka wytrzymałość na zginanie, rozciąganie i ściskanie
- Duża sztywność konstrukcji przy stosunkowo niewielkiej wadze
- Odporność na uszkodzenia mechaniczne i chemiczne
Wytrzymałość profili zimnogiętych może się różnić w zależności od ich wymiarów i kształtu. Dla przykładu, wytrzymałość na zginanie dla różnych profili zamkniętych może wynosić:
- Profil 50x50x5 mm: około 45 kN
- Profil 80x80x6 mm: około 72 kN
- Profil 100x100x8 mm: około 117 kN
- Profil 120x120x10 mm: około 180 kN
Profile zimnogięte to elementy konstrukcyjne wytwarzane przez gięcie blachy na zimno, co pozwala uzyskać kształty takie jak ceowniki, zetowniki, kątowniki, teowniki czy omega. Ze względu na ich wytrzymałość, lekkość i łatwość montażu, znajdują szerokie zastosowanie w wielu dziedzinach budownictwa i przemysłu.
Tak, perforowane kasetony elewacyjne to jedna z dostępnych opcji wykończenia, która oferuje dodatkowe korzyści estetyczne i funkcjonalne. Perforacja kasetonów elewacyjnych polega na wykonaniu w nich otworów w procesie wykrawani lub cięcia laserowego.
Zalety perforowanych kasetonów elewacyjnych
- Estetyka: Perforacja pozwala na tworzenie unikalnych wzorów i efektów wizualnych na elewacji budynku.
- Kontrola światła: Otwory w kasetonach umożliwiają częściowe przepuszczanie światła, co może być wykorzystane do tworzenia interesujących efektów świetlnych.
- Wentylacja: Perforacja może poprawić cyrkulację powietrza w systemie elewacji wentylowanej.
- Akustyka: Perforowane kasetony mogą przyczynić się do lepszej izolacji akustycznej budynku.
- Lekkość konstrukcji: Perforacja zmniejsza wagę kasetonów, co może być korzystne w niektórych projektach.
Perforacja blachy to proces polegający na wykonywaniu otworów o określonym kształcie i rozmieszczeniu w arkuszach blachy. Jest to technika szeroko stosowana w przemyśle i budownictwie, oferująca wiele korzyści funkcjonalnych i estetycznych.
Obróbki blacharskie są wykonywane z różnych materiałów i w różnych grubościach, w zależności od zastosowania i wymagań projektu. Najczęściej stosowane grubości wynoszą:
- Stal powlekana (ocynkowana z powłoką lakierniczą):
- Grubość: 0,5 mm – 0,7 mm
- To najpopularniejszy materiał do obróbek blacharskich, takich jak obróbki dachowe, wiatrownice, pasy nadrynnowe czy okapy.
- Blacha aluminiowa:
- Grubość: 0,6 mm – 1,0 mm
- Aluminium jest stosowane tam, gdzie ważna jest lekkość i odporność na korozję, np. w okolicach stref narażonych na wilgoć i zasolenie.
- Blacha miedziana:
- Grubość: 0,55 mm – 0,8 mm
- Stosowana głównie w budownictwie zabytkowym lub ekskluzywnym, gdzie istotny jest wygląd i trwałość.
- Blacha tytanowo-cynkowa:
- Grubość: 0,7 mm – 0,8 mm
- Często wykorzystywana w nowoczesnych konstrukcjach oraz na dachach z dużymi wymaganiami estetycznymi.
- Blacha nierdzewna (inox):
- Grubość: 0,5 mm – 0,8 mm
- Używana tam, gdzie ważna jest wysoka odporność na korozję i trwałość, np. w obiektach przemysłowych.
Dobór grubości zależy od:
- Przewidywanego obciążenia (np. wiatrem, śniegiem).
- Rodzaju konstrukcji i miejsca montażu.
- Estetyki i wytrzymałości materiału.
W praktyce, najczęściej stosowaną grubością obróbek blacharskich w budownictwie mieszkaniowym jest 0,5 mm dla blach stalowych powlekanych.
Tak, nasz dział techniczny służy pełną pomocą w doborze produktu, jego przygotowaniu i dopasowaniu do wymogów klienta.
Kasetony można wykonać w dowolnej palecie RAL, zarówno w lakierach matowych jak i w połysku.
Paleta kolorów RAL to międzynarodowy standard oznaczania barw, szeroko stosowany w przemyśle i budownictwie. System ten, opracowany w Niemczech w 1927 roku, zawiera kilka tysięcy precyzyjnie zdefiniowanych kolorów, z których każdy ma przypisany unikalny kod numeryczny.
Malowanie proszkowe kasetonów elewacyjnych jest korzystnym rozwiązaniem z kilku istotnych powodów:
- Trwałość i odporność
Powłoka uzyskana w procesie malowania proszkowego charakteryzuje się wyjątkową trwałością i odpornością na różnorodne czynniki:
- Uszkodzenia mechaniczne
- Korozję
- Warunki atmosferyczne
- Promieniowanie UV
- Wilgoć
- Chemikalia
Dzięki temu kasetony elewacyjne zachowują swój estetyczny wygląd przez długi czas, nawet do 15-20 lat6. Jest to szczególnie ważne w przypadku elementów narażonych na ciągłe działanie czynników zewnętrznych.
- Estetyka
Malowanie proszkowe pozwala uzyskać:
- Idealnie gładką i jednolitą powierzchnię
- Szeroką gamę kolorów i wykończeń (mat, połysk, satyna)
- Możliwość tworzenia efektów specjalnych, np. imitacji metali szlachetnych
Dzięki temu kasetony elewacyjne mogą być idealnie dopasowane do projektu architektonicznego, podnosząc walory estetyczne całego budynku.
- Ekologia i ekonomia
Malowanie proszkowe jest przyjazne dla środowiska:
- Nie zawiera rozpuszczalników
- Nie emituje szkodliwych substancji
- Umożliwia ponowne wykorzystanie nadmiaru proszku
Dodatkowo, proces ten jest ekonomiczny ze względu na niskie zużycie materiału i długotrwałość uzyskanej powłoki.
- Izolacja termiczna i akustyczna
Kasetony elewacyjne pokryte farbą proszkową przyczyniają się do poprawy izolacji termicznej i akustycznej budynku, co przekłada się na niższe koszty ogrzewania i większy komfort użytkowania.
Kasetony elewacyjne stalowe są wykorzystywane ze względu na swoje liczne zalety, takie jak:
- długa żywotność oraz odporność na uszkodzenia mechaniczne,
- szybki, łatwy i przystępny cenowo montaż oraz demontaż,
- doskonała izolacja budynków przed nagrzewaniem się i stratą ciepła,
- nowoczesny design i harmonijne połączenia dzięki niewidocznym mocowaniom,
- możliwość wykonania różnych wzorów perforacji.
Proces montażu kasetonów elewacyjnych aluminiowych i stalowych zaczyna się od przygotowania podkonstrukcji, czyli konsoli i profili, które tworzą stelaż dla paneli. Następnie instalowana jest izolacja, obróbki blacharskie wokół okien, drzwi i innych elementów oraz siatki wentylacyjne. Na końcu montowane są kasetony elewacyjne aluminiowe i stalowe za pomocą poziomych łączników i listew startowych, zapewniających stabilne oparcie. Prawidłowo zamontowane panele są odporne na warunki atmosferyczne, w tym wiatr.
Tak, kasetony elewacyjne mogą być elementem elewacji wentylowanej. Stanowią one jedną z opcji wykończenia zewnętrznego w systemie elewacji wentylowanych.
Kasetony elewacyjne pełnią rolę zewnętrznej okładziny w systemie elewacji wentylowanej. Są one montowane na konstrukcji nośnej, która jest kotwiona do ściany budynku. Taka konstrukcja umożliwia stworzenie szczeliny wentylacyjnej między okładziną a warstwą izolacji termicznej, co jest kluczowym elementem elewacji wentylowanej.
Elewacje wentylowane to starannie zaprojektowane fasady budynków, które składają się z metalowego stelażu i zamontowanych na nim paneli. Między ścianą a elewacją znajduje się szczelina wentylacyjna, pozwalająca na swobodny przepływ powietrza, co chłodzi budynek podczas gorących dni. Dodatkowo, można tam umieścić izolację cieplną, która pomaga utrzymać ciepło w chłodniejszych miesiącach.
Koszt szkolenia to 100 zł + VAT. Warunkiem udziału w szkoleniach jest wpłata kwoty 100 zł netto + 23% VAT na konto PG Group
24 1090 2590 0000 0001 4505 5887 z dopiskiem:
„wpłata za udział w szkoleniu dnia …„
z podaniem dokładnej daty szkolenia. Do zaksięgowanej wpłaty wystawimy fakturę zaliczkową oraz końcową po odbytym szkoleniu. Szkolenie zakończone jest wydaniem Certyfikatu uprawniającego do montażu naszych konstrukcji.
Szkolenia odbywają się w siedzibie firmy, pod podanym niżej adresem.
W celu ustalenia terminu szkolenia prosimy o kontakt z Biurem obsługi klienta
Planowany czas szkolenia – 6 godzin.
PG Group sp. z o.o.
Nowa Wieś Wrocławska
Relaksowa 41
55-080 Kąty Wrocławskie
- Omówienie konstrukcji PG Group
- Omówienie konstrukcji wolnostojących z podziałem na konstrukcje standardowe i bifacjalne, w tym:
- Rodzaje konstruckji ze względu na układ i wielkość modułów PV
- Różnica między konstrukcją dla paneli standardowych a bifacjalnych
- Konstrukcje dla farm fotowoltaicznych
- Zasady montażu konstrukcji
- Omówienie konstrukcji na dachy płaskie z omówieniem realnych przypadków w tym:
- Dobór konstrukcji na dach płaski
- Wyznaczanie stref wiatrowych, w obrębie których można montować konstrukcje
- Zasady wyznaczania stref montażu i odstępów między rzędami
- Techniczne aspekty dachów płaskich wykonanych z membrany pod względem budowy instalacji PV:
- Czy można dziurawić dachy płaskie?
- Jak przygotować dach wykonany z membrany do montażu?
- Czy konstrukcja zgrzewana jest lepsza niz balastowa?
- Czy konstrukcja zgrzewana wytrzyma obciążenie wiatrem?
- Jak zamontować konstrukcję zgrzewaną na dachu płaskim wykonanym z membrany – omówienie montaży konstrukcji dachowych na dachach płaskich wykonanych z membrany
- Ćwiczenia praktyczne zgrzewania konstruckji do membrany PCV i bitumicznej
Na szkoleniu zaprezentowane zostaną wszystkie systemy konstrukcyjne produkowane przez PG Group, ze szczegółowym omówieniem systemów na dach płaski, w tym systemów zgrzewanych, balastowych, inwazyjnych w układzie wschód-zachód oraz południe.
Uczestnicy zostaną przeszkoleni w zakresie montażu konstrukcji PG Group, z naciskiem na konstrukcje dla dachów płaskich. Zostaną zaprezentowane zasady montażu konstrukcji PV na dachach płaskich wykonanych z membrany oraz zostaną przeprowadzone ćwiczenia praktyczne zgrzewania membrany przy pomocy zgrzewarki.