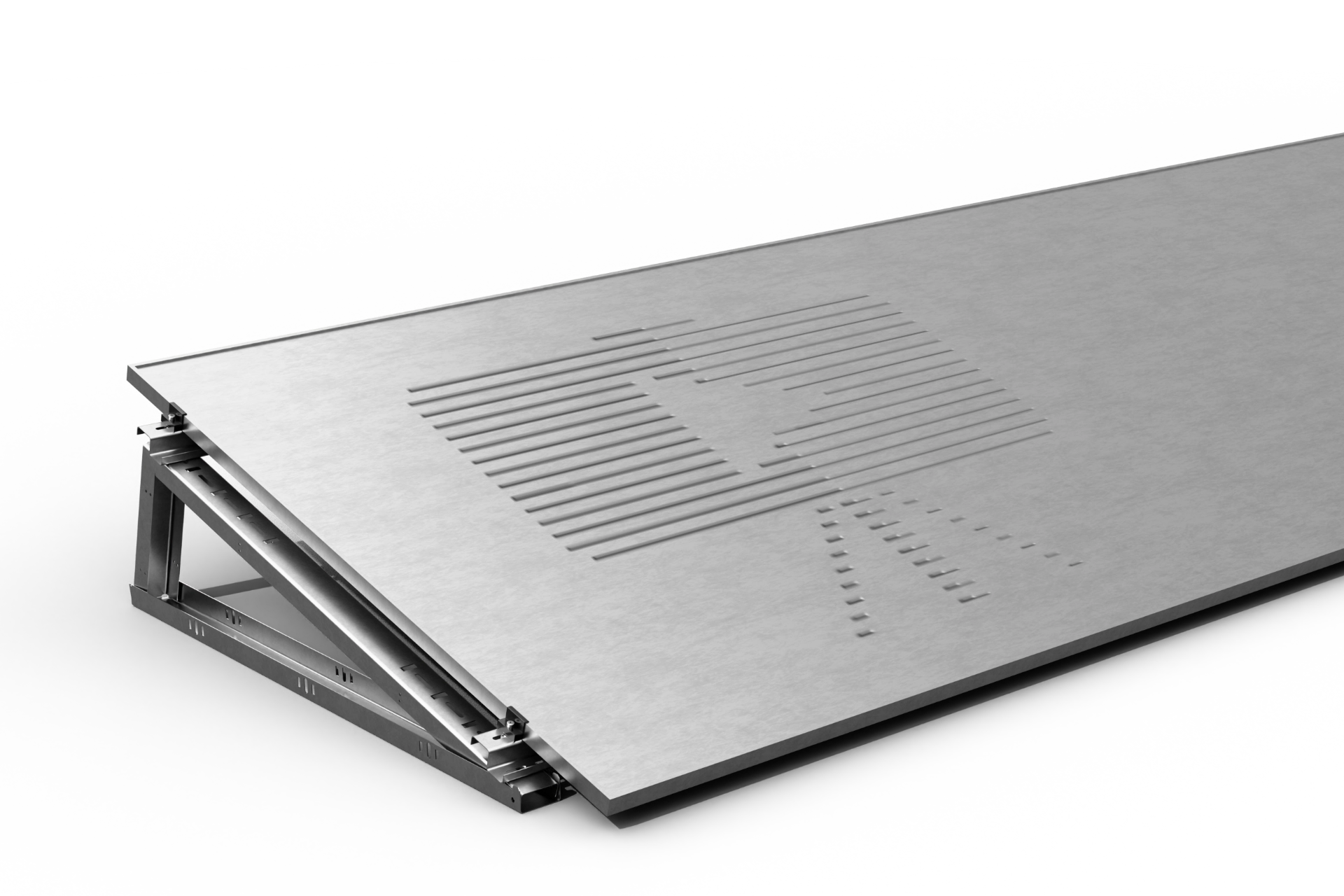
Szkolenia
Nasze szkolenia skupiają się głównie na produktach. Obejmują one omówienie różnych wariantów i modyfikacji, a także technik montażu oraz instalacji. Zachęcamy również do dzielenia się własnymi pomysłami, które możemy dostosować do projektu. Prowadzimy je w otwartej formule! 🙂
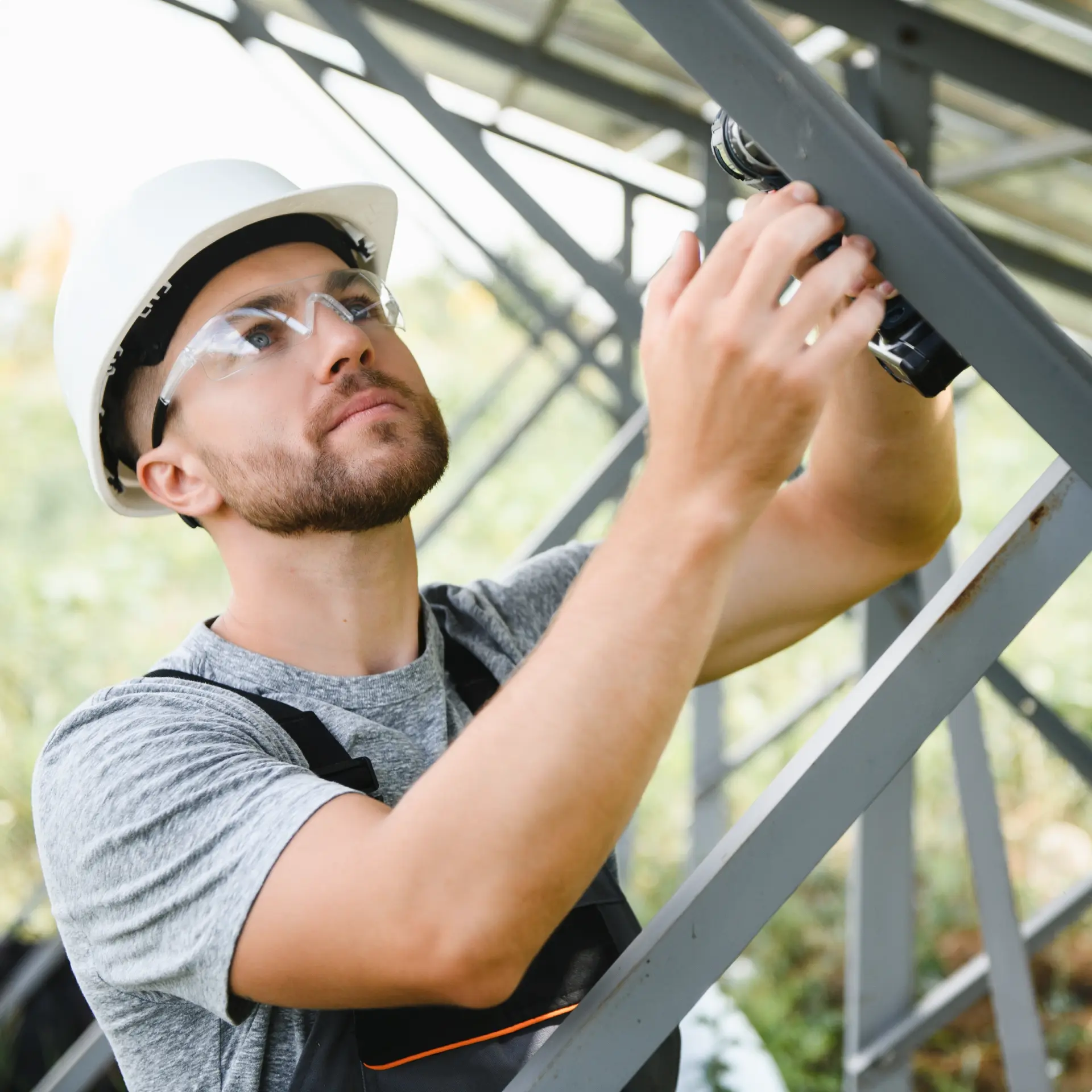
Bezbłędna instalacja systemów montażowych
Zależy nam na tym, żeby produkowane przez nas konstrukcje PV były montowane w profesjonalny i właściwy sposób. Dlatego zakres szkoleń jest zawsze dostosowywany indywidualnie do potrzeb i wymagań danego klienta oraz projektu.
Aby ułatwić pracę instalatorom i monterom prowadzimy szczegółowe szkolenia dotyczące montażu każdego rodzaju naszych konstrukcji. Omawiamy sposoby mocowania na różnych powierzchniach, definiujemy zagrożenia i porównujemy niuanse.
Korzyści
Poznasz nasze produkty: ich konstrukcje, rodzaje, warianty i sposób montażu
Zdobyte przez Ciebie kwalifikacje będą gwarantem utrzymania warunków gwarancji
Otrzymasz certyfikat instalatora PG Group, napijesz się najlepszej kawy i zobaczysz nasz zakład 🙂
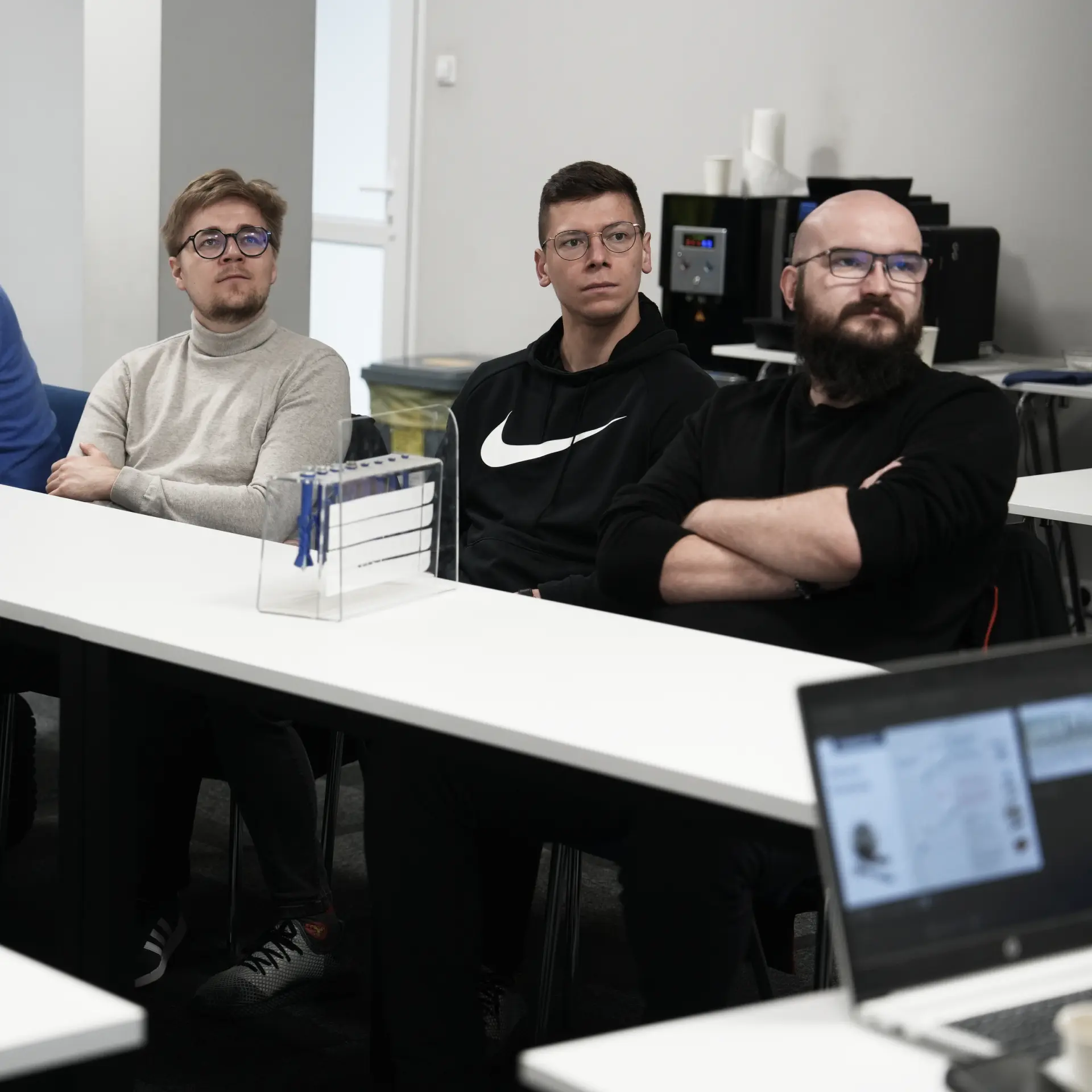
Jako czołowy producent systemów montażowych jesteśmy zobowiązani do przestrzegania obowiązujących przepisów i norm budowlanych. Jesteśmy na bieżąco z obowiązującym prawem, ale śledzimy też najnowsze trendy branżowe. W związku z tym sami regularnie uczestniczymy w szkoleniach naszych partnerów biznesowych jak Rawlplug (lider w produkcji zamocowań), czy Protan (lider w produkcji pokryć dachowych).
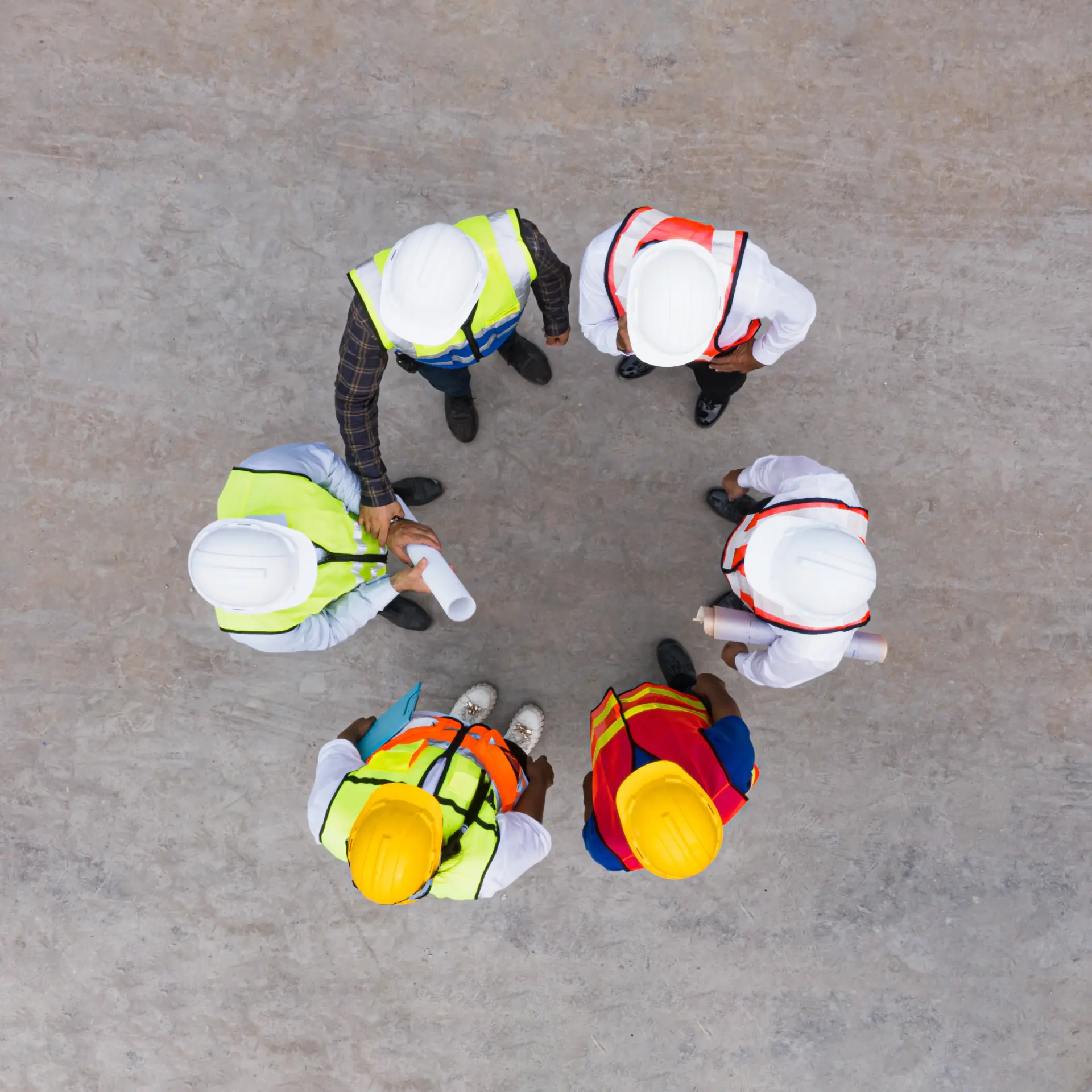
Czy na dachu płaskim lepiej stosować system inwazyjny czy nieinwazyjny? Jak bezpiecznie zamontować konstrukcję na grząskim gruncie? Czym różni się PosMAC, Granite® i Magnelis®?
Tak – nasz zakład znajduje się tuż przy Wrocławiu, w Nowej Wsi Wrocławskiej dzięki czemu obsługujemy klientów z całego Dolnego Śląska. Oferujemy profesjonalne gięcie blach we Wrocławiu, w tym gięcie na prasach krawędziowych CNC dla firm przemysłowych, konstrukcyjnych i produkcyjnych. Lokalizacja przy głównych trasach umożliwia nam szybki odbiór i dostawę elementów, co znacząco skraca czas realizacji zamówień dla partnerów z Wrocławia i okolic.
Tak – gięcie blach na prasach CNC to technologia, która gwarantuje bardzo wysoką powtarzalność. Raz ustawiony program pozwala formować setki identycznych detali, co jest kluczowe dla klientów z branży produkcyjnej i konstrukcyjnej. Automatyzacja procesu eliminuje ryzyko błędów ludzkich, a systemy pomiarowe w maszynach zapewniają utrzymanie jednakowych parametrów nawet przy dużych seriach produkcyjnych.
Gięcie na prasach krawędziowych pozwala formować różnorodne gatunki blach. Najczęściej realizujemy:
- stal konstrukcyjną (tzw. czarną),
- stal nierdzewną i kwasoodporną,
- aluminium,
- miedź i mosiądz.
Każdy z materiałów wymaga indywidualnego doboru siły nacisku i narzędzi, aby uzyskać oczekiwany kąt i promień gięcia. Dzięki sterowaniu komputerowemu CNC gwarantujemy powtarzalność efektu niezależnie od rodzaju metalu.
PG Group dysponuje rozbudowanym parkiem maszynowym i doświadczoną kadrą specjalistów, co gwarantuje wysoką jakość oraz terminowość usług. Korzystamy z zaawansowanych laserów Trumpf TruLaser 3060 i TruLaser 1030 o dużej mocy, a także kombinowanego lasera z wykrawarką TruMatic 6000 – to pozwala nam realizować nawet nietypowe zlecenia, łącząc cięcie z perforacją czy przetłaczaniem. Pracujemy na formatach blach do 6000 x 2500 mm i ciężarze nawet 3 ton, więc jesteśmy w stanie ciąć wielkogabarytowe arkusze oraz całe serie elementów jednocześnie. Stawiamy na najwyższą precyzję (nasze maszyny osiągają dokładność rzędu ±0,03 mm) i efektywność – automatyzacja produkcji umożliwia szybkie wykonanie zleceń przy zachowaniu ścisłych tolerancji. Wybierając naszą ofertę, zyskujesz pewność jakości potwierdzonej doświadczeniem i referencjami wielu zadowolonych klientów. Zapewniamy doradztwo techniczne na każdym etapie – od optymalizacji projektu pod cięcie laserowe, po finalną realizację i dostawę. Jeśli szukasz cięcia laserowego we Wrocławiu lub okolicach, nasza firma to sprawdzony partner, który zrealizuje Twoje zamówienie fachowo, szybko i w konkurencyjnej cenie.
Cena usługi cięcia laserowego zależy od kilku czynników, przede wszystkim od rodzaju i grubości materiału, a także od złożoności kształtu oraz wielkości zamówienia (liczby wycinanych elementów). Generalnie im grubszy i twardszy materiał, tym wolniej przebiega cięcie – co wpływa na wyższą cenę ze względu na dłuższy czas pracy lasera. Również skomplikowane detale z dużą liczbą otworów czy konturów wydłużają czas cięcia w porównaniu do prostych kształtów. Na koszt wpływa także wielkość serii – przy większych zamówieniach jednostkowa cena za cięcie może być niższa dzięki efektowi skali. Każde zlecenie wyceniamy indywidualnie, biorąc pod uwagę powyższe parametry, aby zaproponować konkurencyjną stawkę. Zachęcamy do kontaktu – nasi specjaliści szybko przygotują bezpłatną wycenę dla Twojego projektu cięcia laserowego. Dzięki temu poznasz dokładny koszt realizacji zanim zlecisz nam usługę.
Maksymalna grubość cięcia zależy od mocy lasera oraz rodzaju materiału. Nasze przemysłowe wycinarki laserowe potrafią przeciąć bardzo grube blachy – w przypadku stali konstrukcyjnej nawet do około 25 mm grubości, zaś dla stali nierdzewnej do ok. 30 mm. Aluminium ze względu na swoje właściwości tniemy laserowo do około 15–20 mm, a miedź i mosiądz do kilkunastu mm. Dla arkuszy blach powyżej tych grubości zazwyczaj stosuje się już inne metody (np. cięcie plazmowe), ponieważ laser traci wtedy efektywność. W praktyce zdecydowana większość elementów w przemyśle mieści się w zakresach grubości obsługiwanych przez nasze lasery. Chętnie pomożemy zweryfikować, czy Twój materiał i grubość nadają się do cięcia laserowego – wystarczy przesłać zapytanie z parametrami.
- Stal nierdzewna: 30 mm
- Stal węglowa: 25 mm
- Aluminium: 25 mm
- Miedź: 15 mm
Te wartości są osiągalne na maszynie TruLaser 3060, która oferuje największe możliwości cięcia spośród wymienionych urządzeń.
Cięcie laserowe jest bardzo uniwersalne – można nim ciąć większość metali używanych w przemyśle. Najczęściej laserem tnie się stal konstrukcyjną (tzw. stal czarną), stal nierdzewną i kwasoodporną, a także aluminium oraz metale kolorowe, takie jak miedź czy mosiądz. Nowoczesne lasery światłowodowe radzą sobie nawet z materiałami wysoko refleksyjnymi (typu mosiądz, miedź) dzięki specjalnym technologiom wiązki. W dodatku laserem CO₂ można ciąć także niemetale – np. tworzywa sztuczne, sklejkę drewnianą czy tekstylia – jednak w naszej ofercie skupiamy się na precyzyjnym cięciu elementów blaszanych i metalowych. Jeśli nie masz pewności, czy dany materiał da się ciąć laserowo, skontaktuj się z nami – doradzimy najlepsze rozwiązanie.
PG Group przeszło wszystkie kroki potrzebne do spełnienia warunków normy środowiskowej ISO 14001 i posiada certyfikację. Aby uzyskać normę środowiskową ISO 14001, firma musiała spełnić następujące warunki:
Wdrożenie Systemu Zarządzania Środowiskowego (SZŚ)
- Przeprowadzenie audytu wstępnego w celu oceny obecnego stanu organizacji.
- Opracowanie i wdrożenie udokumentowanego systemu SZŚ, w tym:
- Polityki środowiskowej
- Procedur systemowych
- Instrukcji operacyjnych
- Identyfikacja i ocena aspektów środowiskowych związanych z działalnością firmy.
- Określenie celów i zadań środowiskowych zgodnych z polityką firmy.
- Zapewnienie zgodności z obowiązującymi przepisami prawnymi dotyczącymi ochrony środowiska.
Funkcjonowanie systemu
- Zapewnienie zaangażowania kierownictwa w budowanie i utrzymanie SZŚ.
- Wdrożenie podejścia procesowego i cyklu PDCA (Planuj-Wykonaj-Sprawdź-Działaj).
- Prowadzenie monitoringu i pomiarów kluczowych parametrów środowiskowych.
- Szkolenie pracowników z zakresu wymagań normy ISO 14001 i wdrożonych procedur.
- Wdrożenie sterowania operacyjnego dla procesów związanych ze znaczącymi aspektami środowiskowymi.
- Opracowanie i wdrożenie procedur reagowania na sytuacje awaryjne.
Certyfikacja
- Przeprowadzenie audytu wewnętrznego w celu weryfikacji zgodności z wymaganiami normy.
- Podjęcie działań korygujących i zapobiegawczych w przypadku wykrycia niezgodności.
- Przejście audytu certyfikującego przeprowadzonego przez akredytowaną jednostkę certyfikującą.
PG Group spełnia wymagania zgodne z normą EN 1090 i posiada certyfikację Firma musiała przejść przez następujące etapy:
Wdrożenie Systemu Zakładowej Kontroli Produkcji (ZKP)
- Opracowanie i wdrożenie udokumentowanego systemu Zakładowej Kontroli Produkcji (ZKP).
- System ZKP powinien obejmować wszystkie procesy specjalne stosowane w produkcji, takie jak:
- Projektowanie (jeśli firma prowadzi taki proces)
- Spawanie
- Zabezpieczenie przed korozją
- Łączenie z wykorzystaniem łączników mechanicznych
- Kontrola i badania
- Zapewnienie odpowiedniego personelu, wyposażenia i procedur dla zapewnienia zgodności wyrobu.
Spełnienie wymagań technicznych
- Spełnienie wymagań technicznych określonych w normie EN 1090-2 dla konstrukcji stalowych lub EN 1090-3 dla konstrukcji aluminiowych.
- Przeprowadzenie pierwszego badania typu (ITT) i pierwszych obliczeń typu (ITC) dla produktów.
- Zapewnienie jakości spawania zgodnie z normą ISO 3834 (część 2, 3 lub 4).
Certyfikacja
- Przejście wstępnej inspekcji zakładowej kontroli produkcji przeprowadzonej przez akredytowaną jednostkę notyfikowaną.
- Pozytywne przejście audytu certyfikującego obejmującego pełny zakres systemu ZKP.
- Uzyskanie certyfikatu systemu Zakładowej Kontroli Produkcji oraz Certyfikatu dla Spawalnictwa.
Dodatkowe wymagania
- Posiadanie wykwalifikowanego personelu, w tym spawaczy z odpowiednimi uprawnieniami.
- Zapewnienie odpowiedniego wyposażenia do produkcji, pomiarów i kontroli.
- Wdrożenie systemu nadzoru nad dokumentacją i zapisami.
- Opracowanie i stosowanie procedur oceny zgodności wyrobu.
Obecny certyfikat zgodności z normą EN 1090 jest ważny do 12.12.2026 r.
Perforacja blachy to proces tworzenia regularnych otworów w blachach metalowych, które mogą mieć różne kształty, rozmiary i wzory. Otwory te są zwykle rozmieszczone w ustalonym układzie (np. rzędowym, mijankowym lub innym). Perforacja jest wykonywana w celu nadania blachom określonych właściwości funkcjonalnych, estetycznych lub technologicznych.
Cechy perforacji:
- Kształt otworów: Okrągłe, kwadratowe, prostokątne, sześciokątne, dekoracyjne (np. wzory nieregularne).
- Układ otworów: Regularny (symetryczny) lub nieregularny, w rzędach prostych lub przesuniętych.
- Wielkość otworów: Od bardzo drobnych (np. poniżej 1 mm) po duże (kilka centymetrów).
- Stopień perforacji: Procentowy udział powierzchni otworów w całkowitej powierzchni blachy.
Metody perforacji blachy:
- Mechaniczna (prasa perforacyjna):
- Najczęściej stosowana metoda w przemyśle, wykorzystująca matryce i stemple.
- Laserowa:
- Umożliwia precyzyjne wycinanie dowolnych wzorów, szczególnie w produkcji niestandardowej.
- Wodne cięcie (hydro cutting):
- Używane do skomplikowanych kształtów i materiałów trudnych do obróbki.
- Chemiczna (trawienie):
- Stosowana głównie w przypadku cienkich blach i delikatnych wzorów.
Zastosowania perforowanych blach:
- Wentylacja i przepuszczalność:
- W systemach wentylacyjnych, klimatyzacyjnych i filtracyjnych.
- Design i architektura:
- Fasady budynków, ekrany akustyczne, sufity podwieszane, balustrady, elementy dekoracyjne.
- Przemysł i technologia:
- Sita w maszynach, osłony, podesty robocze, panele akustyczne.
- Zastosowania ochronne:
- Kraty ochronne, osłony maszyn, zabezpieczenia antywłamaniowe.
- Rolnictwo i przemysł spożywczy:
- Elementy maszyn do sortowania, suszenia lub obróbki produktów.
Dzięki perforacji blacha może łączyć lekkość z wytrzymałością i funkcjonalnością, co czyni ją niezwykle wszechstronnym materiałem.